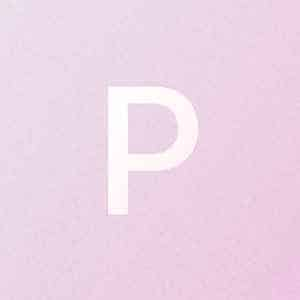
Pembio
A curated collection of resources, worksheets and templates within the productivity space.
Get the app ✌️The 10 most popular productivity methods
Productivity is a key aspect of personal and professional success.
It allows us to accomplish more tasks in less time, and to achieve our goals with greater efficiency and effectiveness.
Over the years, many different productivity methods have been developed, each with its own unique approach and set of tools and techniques.
In this article, we will explore the 10 most popular productivity methods, and discuss the key features, advantages, and limitations of each one. Whether you are a busy student, a hardworking employee, or a passionate entrepreneur, there is sure to be a productivity method that suits your needs and preferences. Let's dive in and discover the secrets of boosting your productivity.
- 1. Pomodoro Technique
- 2. 80/20 Rule
- 3. The Eisenhower Matrix
- 4. Kaplan-Norton Balanced Scorecard
- 5. The 5S Method
- 6. GTD Method
- 7. Kanban
- 8. The Lean Method
- 9. Six Sigma
- 10. Kaizen
The Pomodoro Technique:
This method involves breaking work into intervals (called "pomodoros") separated by short breaks.
The Pomodoro Technique is a time management method developed by Francesco Cirillo in the 1980s. The technique is based on the idea of using a timer to break down work into intervals, traditionally 25 minutes in length, separated by short breaks. The technique is named after the tomato-shaped kitchen timer that Cirillo used as a university student.
The Pomodoro Technique has several key principles:
- Choose a task to be accomplished.
- Set the Pomodoro timer (traditionally to 25 minutes).
- Work on the task until the timer rings.
- Take a short break (usually 5 minutes).
- After four Pomodoros, take a longer break (usually 15-30 minutes).
The Pomodoro Technique is designed to help users stay focused on their work, avoid burnout, and improve their productivity. It encourages frequent breaks, which can help to prevent fatigue and maintain a high level of concentration. The technique is simple to use and can be applied to a wide range of tasks and activities. However, some people may find it difficult to stick to the strict time intervals, and may need to adjust the technique to suit their individual needs and preferences.
The 80/20 rule:
The 80/20 rule, also known as the Pareto principle, is a well-known concept in productivity and time management. It is based on the observation that in many cases, roughly 80% of the effects come from 20% of the causes. In other words, a small minority of inputs or efforts tend to produce the majority of the results.
The 80/20 rule has several implications for productivity:
- It suggests that we should focus on the most important tasks and activities, rather than wasting time on low-value tasks that yield little benefit.
- It suggests that we should look for leverage points and leverage activities, where a small amount of effort can produce a large amount of results.
- It suggests that we should look for ways to eliminate or delegate the low-value tasks that consume a disproportionate amount of our time and energy.
- The 80/20 rule is a useful framework for analyzing and optimizing our productivity, but it is not a hard and fast rule. In some cases, the ratio may be different (e.g. 90/10 or 70/30), and it may vary from one situation to another. The key is to apply the principle in a flexible and adaptable way, and to continuously seek ways to improve our productivity and achieve our goals.
The Eisenhower Matrix:
The Eisenhower Matrix, also known as the Eisenhower Decision Matrix, is a tool for prioritizing tasks and activities based on their importance and urgency. It was developed by Dwight D. Eisenhower, the 34th President of the United States, who was known for his organizational skills and effective leadership.
The Eisenhower Matrix consists of a grid with four quadrants, each representing a different type of task or activity:
- Quadrant 1: Important and Urgent tasks (e.g. deadlines, crises, emergencies)
- Quadrant 2: Important but Not Urgent tasks (e.g. long-term goals, strategic planning, personal development)
- Quadrant 3: Not Important but Urgent tasks (e.g. distractions, interruptions, trivial tasks)
- Quadrant 4: Not Important and Not Urgent tasks (e.g. time-wasting activities, unimportant tasks)
The Eisenhower Matrix is a useful tool for prioritizing tasks and activities based on their relative importance and urgency. It helps users to focus on the most important tasks, and to avoid getting bogged down by low-value activities that consume time and energy without yielding significant results. It can be used in a variety of contexts, from personal time management to business decision-making. However, it is important to remember that the matrix is only a guide, and that users should adapt it to their individual needs and preferences.
The Kaplan-Norton Balanced Scorecard:
The Kaplan-Norton Balanced Scorecard is a performance management system developed by Robert S. Kaplan and David P. Norton in the 1990s. It is based on the idea of using a balanced set of performance measures to track and improve organizational performance.
The Kaplan-Norton Balanced Scorecard has four main perspectives:
- Financial perspective: This perspective focuses on financial performance and profitability. It includes measures such as revenue, costs, profits, and shareholder value.
- Customer perspective: This perspective focuses on customer satisfaction and loyalty. It includes measures such as customer satisfaction, retention, and referrals.
- Internal business processes perspective: This perspective focuses on the internal processes and activities that drive performance. It includes measures such as efficiency, effectiveness, and innovation.
- Learning and growth perspective: This perspective focuses on the human, organizational, and technological capabilities that enable the organization to improve and adapt. It includes measures such as training, development, and technology.
The Kaplan-Norton Balanced Scorecard is a comprehensive and flexible performance management system. It provides a balanced and integrated view of organizational performance, and helps managers to align strategies, objectives, and measures across the organization. However, it can be complex and time-consuming to implement, and it may require significant resources and effort to maintain and update.
The 5S Method:
The 5S method is a productivity and organization system that originated in Japan. It is based on the Japanese words seiri (sort), seiton (set in order), seiso (shine), seiketsu (standardize), and shitsuke (sustain), which represent the five steps of the method.
The 5S method has the following steps:
- Sort: This step involves sorting through the items in a workspace and removing any unnecessary or unused items.
- Set in order: This step involves organizing the remaining items in a logical and accessible manner, so that they can be easily found and used.
- Shine: This step involves cleaning and maintaining the workspace, so that it is clean, safe, and efficient.
- Standardize: This step involves establishing clear rules and procedures for maintaining the clean and organized workspace, and for identifying and correcting any problems or deviations.
- Sustain: This step involves maintaining the improvements achieved through the previous steps, and continuously seeking ways to improve the workspace and the processes that take place in it.
The 5S method is a simple and effective tool for improving productivity and organization. It can be applied to a wide range of settings, from office environments to manufacturing plants. It is particularly useful for reducing waste, improving safety, and enhancing the overall quality of the workplace. However, it requires commitment and discipline to implement and sustain, and it may require training and support to be successful.
The GTD Method:
The GTD (Getting Things Done) method is a productivity system developed by David Allen. It is based on the idea of capturing, clarifying, organizing, and reviewing all the tasks, projects, and commitments that demand our attention, in order to reduce stress and improve productivity.
The GTD method has the following steps:
- Capture: This step involves collecting and capturing all the tasks, ideas, and information that demand our attention, in a trusted and accessible system.
- Clarify: This step involves processing and clarifying the collected items, by deciding what action is required for each item, and by breaking down larger projects into smaller and more manageable tasks.
- Organize: This step involves organizing the processed items, by assigning them to the appropriate categories, contexts, and time frames.
- Reflect: This step involves regularly reviewing and reflecting on the organized items, to ensure that they are up to date, relevant, and aligned with our goals and priorities.
- Engage: This step involves taking action on the organized items, by working on them, delegating them, or deferring them as appropriate.
- The GTD method is a comprehensive and flexible productivity system. It provides a clear and structured approach to managing tasks, projects, and commitments, and it helps users to reduce stress, improve focus, and increase productivity. However, it can be complex and time-consuming to implement, and it may require significant effort and practice to master.
The Kanban Method:
The Kanban method is a productivity and project management system that originated in Japan. It is based on the principles of lean manufacturing, and it is designed to help organizations to improve their efficiency, flexibility, and responsiveness.
The Kanban method has the following key elements:
- Visualize: This element involves creating a visual representation of the workflow, by dividing it into different stages or columns, and by using cards or other visual indicators to represent the tasks or items that move through the workflow.
- Limit work in progress: This element involves setting limits on the number of tasks or items that can be in progress at each stage of the workflow, in order to avoid overloading the system and to improve the flow of work.
- Manage flow: This element involves continuously monitoring and managing the flow of work through the system, by identifying and addressing any bottlenecks or disruptions that may occur.
- Make process policies explicit: This element involves defining and communicating the rules and policies that govern the workflow, in order to ensure consistency and predictability.
- Improve collaboratively: This element involves involving all stakeholders in the continuous improvement of the system, by using feedback and data to identify and implement changes that can enhance the flow of work and the overall performance of the organization.
The Kanban method is a powerful and effective tool for managing projects and improving productivity. It is particularly useful for organizations that need to adapt to changing environments and requirements, and that need to maintain a high level of flexibility and responsiveness. However, it may require training and support to implement successfully, and it may not be suitable for all types of organizations or projects.
The Lean Method:
The Lean method is a productivity and management system that originated in Japan, and that has been widely adopted in many different industries and organizations around the world. It is based on the principles of lean manufacturing, which were developed by Toyota Motor Corporation to improve the efficiency and quality of its manufacturing processes.
The Lean method has several key principles:
- Identify and eliminate waste: This principle involves identifying and eliminating any activities or processes that do not add value to the customer, and that consume resources without generating benefits.
- Empower and engage employees: This principle involves empowering and engaging employees in the improvement of the processes and the organization, by involving them in decision-making, problem-solving, and continuous learning.
- Build a culture of continuous improvement: This principle involves establishing a culture of continuous improvement, in which all stakeholders are committed to seeking and implementing ways to improve the processes, the products, and the organization as a whole.
- Focus on the customer: This principle involves focusing on the needs and preferences of the customer, and on providing value to the customer through the products and services offered by the organization.
- Measure and manage performance: This principle involves measuring and managing the performance of the processes and the organization, by using appropriate metrics and by regularly reviewing and improving the performance.
The Lean method is a comprehensive and holistic approach to improving productivity and organizational performance. It is based on a set of principles and practices that can be applied to a wide range of settings, from manufacturing to healthcare, and that can help organizations to achieve excellence and competitive advantage. However, it requires commitment and discipline to implement and sustain, and it may require training and support to be successful.
The Six Sigma Method:
The Six Sigma method is a productivity and quality improvement system that originated in the manufacturing industry, and that has been adopted in many other industries and organizations. It is based on the idea of using data and statistical analysis to identify and eliminate sources of defects and variability in processes, in order to improve the quality of the products and services offered by the organization.
The Six Sigma method has the following key elements:
- Define: This element involves defining the problem or opportunity that the organization wants to address, and establishing the goals and targets for the improvement effort.
- Measure: This element involves collecting and analyzing data to measure the current performance of the process, and to identify the sources of defects and variability.
- Analyze: This element involves using statistical and other analytical tools to understand the causes and patterns of the defects and variability, and to identify potential solutions.
- Improve: This element involves implementing and testing the selected solutions, and verifying that they improve the performance of the process.
- Control: This element involves establishing control mechanisms to maintain the improvements achieved, and to prevent the recurrence of defects and variability.
The Six Sigma method is a powerful and effective tool for improving the quality and productivity of processes. It is particularly useful for organizations that have complex and technical processes, and that need to meet high standards of quality and reliability. However, it can be complex and time-consuming to implement, and it may require specialized training and expertise to use effectively.
The Kaizen Method:
The Kaizen method is a productivity and management system that originated in Japan. It is based on the principle of continuous improvement, which is the belief that small and incremental improvements can add up to significant and lasting results over time.
The Kaizen method has the following key elements:
- Involve all stakeholders: This element involves involving all stakeholders in the improvement effort, including employees, managers, customers, suppliers, and other partners.
- Focus on small and incremental improvements: This element involves focusing on small and incremental improvements, rather than large and disruptive changes. The idea is to make many small changes that can be implemented quickly and easily, and that can add up to significant improvements over time.
- Measure and monitor performance: This element involves measuring and monitoring the performance of the processes and the organization, and using the data to identify areas for improvement and to track the progress of the improvement effort.
- Continuously seek feedback and suggestions: This element involves continuously seeking feedback and suggestions from all stakeholders, and using the feedback to identify opportunities for improvement and to validate the effectiveness of the implemented changes.
- Celebrate and recognize achievements: This element involves celebrating and recognizing the achievements of the improvement effort, and using the success stories to motivate and inspire further improvements.
The Kaizen method is a simple and effective approach to improving productivity and organizational performance. It is based on the principle of continuous improvement, which encourages all stakeholders to be involved in the improvement effort, and to focus on small and incremental changes that can have a positive impact on the organization. However, it requires commitment and discipline to implement and sustain, and it may require training and support to be successful.
By: Johan Flodgren
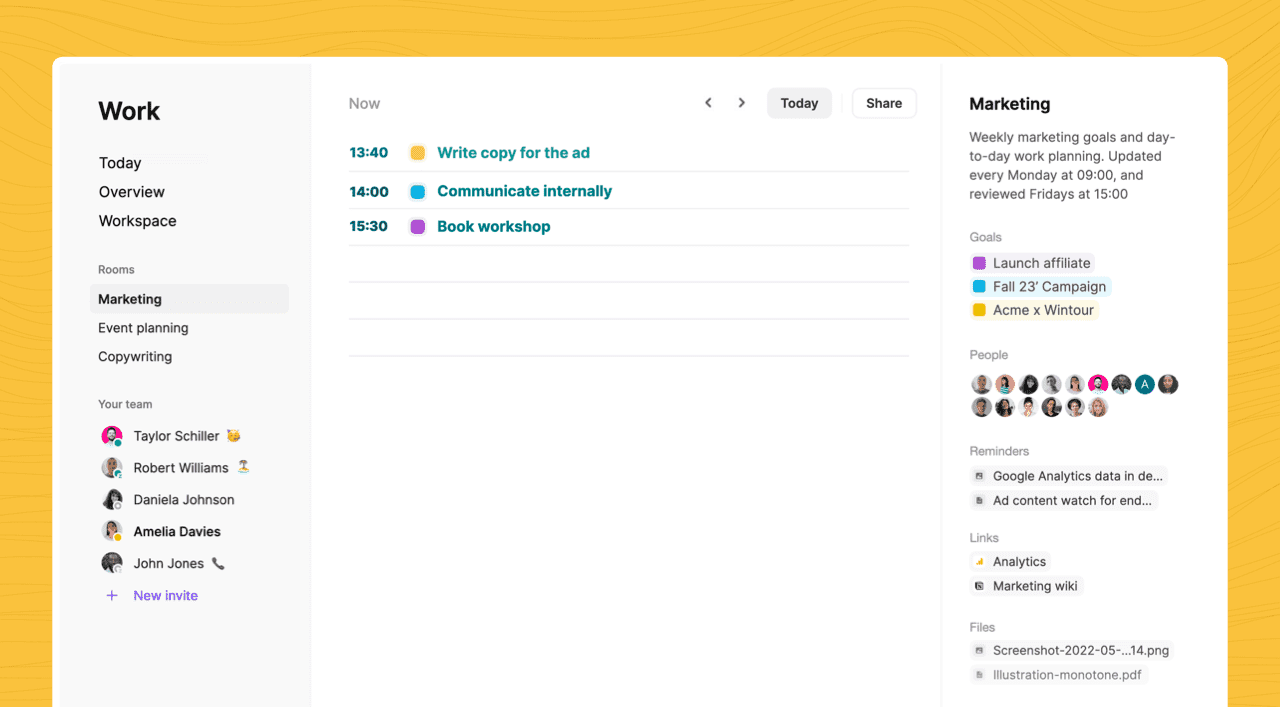
The goal planning app that will skyrocket your productivity
A brand new productivity app - empowering you, or your entire team, to get the most important work done with stunningly simple goal planning.
Get started for free